合板は、3枚以上の薄い木材を接着剤で貼り合わせて作られています。各木材層(プライ)は、通常、木目が隣接する層に対して直角になるように配置されています。これにより、収縮を抑え、完成品の強度が向上します。ほとんどの合板は、建築用に使用される大きな平板にプレス加工されます。また、家具、ボート、航空機などに使用されるため、単純または複合曲線に成形される合板もあります。
薄い木材の層を建築材料として用いるようになったのは、紀元前1500年頃まで遡ります。当時、エジプトの職人たちは、ツタンカーメン王の墓で発見された杉材の棺の外側に、黒檀の薄い板を接着していました。この技法は後にギリシャ人やローマ人によって高級家具やその他の装飾品の製作に用いられました。1600年代には、薄い板で家具を装飾する技法がベニア張りとして知られるようになり、ベニア板自体もベニアと呼ばれるようになりました。
1700年代後半まで、ベニヤ板の切断はすべて手作業で行われていました。1797年、イギリス人のサミュエル・ベンサム卿は、ベニヤ板を製造するための複数の機械に関する特許を出願しました。その特許出願の中で、彼は接着剤を使ってベニヤ板を複数層に重ね合わせ、より厚い板を作るという概念を記述しました。これが、現在私たちが合板と呼んでいるものの、最初の記述です。
このような発展にもかかわらず、家具業界以外で積層ベニアが商業的に利用されるまでには、さらに100年近くかかりました。1890年頃、積層木材は初めてドアの製造に使用されました。需要が高まるにつれ、複数の企業がドアだけでなく、鉄道車両、バス、飛行機にも使用される多層積層木材のシートを生産し始めました。このように使用が増えたにもかかわらず、「貼り合わせた木材」(一部の職人が皮肉を込めてそう呼んだ)を使用するというコンセプトは、製品にマイナスイメージを与えました。このイメージを払拭するため、積層木材メーカーは会合を開き、最終的にこの新しい素材を「合板」と呼ぶことにしました。
1928年、アメリカ合衆国で初めて、一般的な建築資材として4フィート×8フィート(1.2メートル×2.4メートル)の標準サイズの合板が発売されました。その後数十年にわたり、接着剤の改良と新たな製造方法の登場により、合板は幅広い用途に使用できるようになりました。今日では、合板は多くの建築用途で木材に取って代わり、合板製造は数十億ドル規模の世界的な産業となっています。
合板の外側の層はそれぞれ表と裏と呼ばれます。表は実際に使用される表面で、裏は使用されず、隠れた部分です。中心の層はコアと呼ばれます。5層以上の合板では、中間層はクロスバンドと呼ばれます。
合板は、広葉樹、針葉樹、あるいはその両方の組み合わせから作られます。一般的な広葉樹には、トネリコ、メープル、マホガニー、オーク、チークなどがあります。アメリカ合衆国で合板に使用される最も一般的な針葉樹はダグラスファーですが、マツ、スギ、トウヒ、レッドウッドなど、いくつかの種類の針葉樹も使用されています。
複合合板は、パーティクルボードまたは無垢材を端から端まで接合した芯材で構成され、表裏に合板のベニヤ板を貼って仕上げられています。複合合板は、非常に厚い板材が必要な場合に使用されます。
木材の層を接着する接着剤の種類は、完成した合板の用途によって異なります。建物の外装に設置する針葉樹合板には、優れた強度と耐湿性を持つフェノールホルムアルデヒド樹脂が接着剤として使用されるのが一般的です。建物の内装に設置する針葉樹合板には、血液タンパク質または大豆タンパク質接着剤が使用される場合もありますが、現在ではほとんどの針葉樹内装用合板は、外装用合板と同じフェノールホルムアルデヒド樹脂で作られています。内装や家具の製造に使用される広葉樹合板には、通常、尿素ホルムアルデヒド樹脂が使用されています。
用途によっては、表面または裏面(あるいはその両方)にプラスチック、金属、または樹脂を含浸させた紙や布の薄い層を貼り合わせた合板が求められることがあります。これにより、外面の耐湿性や耐摩耗性を高めたり、塗料の付着性を向上させたりすることができます。このような合板はオーバーレイ合板と呼ばれ、建設、輸送、農業などの分野で広く使用されています。
その他の合板シートは、表面に仕上げの外観を与えるために液体ステインでコーティングされていたり、合板の耐火性や耐腐朽性を向上させるためにさまざまな化学薬品で処理されている場合があります。
合板には大きく分けて 2 つのクラスがあり、それぞれ独自の等級分けシステムがあります。
一つは建築用・工業用合板です。このクラスの合板は主に強度が求められ、耐候性と表面・裏面に使用されている単板の等級によって等級が定められています。耐候性は、接着剤の種類によって屋内用または屋外用になります。単板の等級はN、A、B、C、Dのいずれかです。N等級は表面の欠陥が非常に少ないのに対し、D等級は節や割れが多く見られる場合があります。例えば、住宅の床下地に使用される合板は「内装CD」と等級が定められています。これは、表面がC、裏面がDで、接着剤は保護された場所での使用に適していることを意味します。すべての建築用・工業用合板の内側の層は、等級に関わらず、CまたはD等級の単板で作られています。
もう一つの合板の種類は、ハードウッド合板と装飾合板です。この種類の合板は主に外観を重視して使用され、耐湿性の降順で、テクニカル(外装用)、タイプI(外装用)、タイプII(内装用)、タイプIII(内装用)と分類されます。表面のベニヤには、ほとんど欠陥がありません。
サイズ
合板の厚さは、1.6 mm(0.06インチ)から76 mm(3.0インチ)まで様々です。最も一般的な厚さは、6.4 mm(0.25インチ)から19.0 mm(0.75インチ)です。合板の芯材、横木、表裏はそれぞれ異なる厚さの単板で作られる場合もありますが、それぞれの厚さは中央を中心にバランスが取れている必要があります。例えば、表裏は同じ厚さでなければなりません。同様に、上横木と下横木も同じ厚さでなければなりません。
建築現場で使用される合板の最も一般的なサイズは、幅4フィート(1.2m)、長さ8フィート(2.4m)です。その他、幅3フィート(0.9m)と長さ5フィート(1.5m)も一般的です。長さは8フィート(2.4m)から12フィート(3.6m)まで、1フィート(0.3m)刻みで調整可能です。船舶建造などの特殊な用途では、より大きな合板が必要になる場合があります。
合板に使用される木は、一般的に製材に使用される木よりも直径が小さく、ほとんどの場合、合板会社が所有する土地で植林・育成されています。これらの土地は、木の成長を最大限に高め、害虫や火災による被害を最小限に抑えるよう、綿密に管理されています。
以下は、木材を標準的な 4 フィート x 8 フィート (1.2 メートル x 2.4 メートル) の合板シートに加工するための一般的な操作手順です。
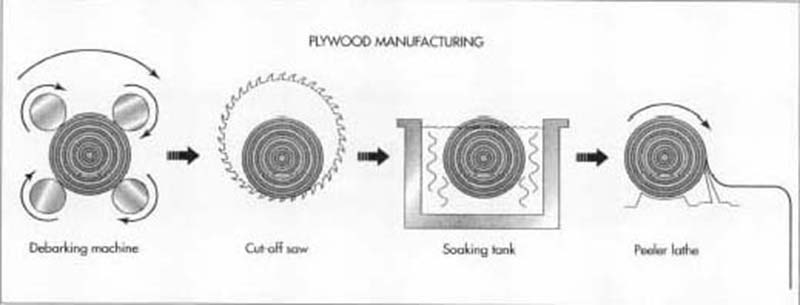
丸太はまず樹皮を剥ぎ、次にピーラーブロックに切断されます。ブロックをベニヤ板に切断するために、まず水に浸し、次にストリップ状に剥がします。
1 ある区域内の選定された樹木は、伐採または伐倒の準備が整ったものとしてマークされます。伐倒は、ガソリン駆動のチェーンソー、またはフェラーと呼ばれる車輪付き車両の前部に取り付けられた大型の油圧式剪断機によって行われます。倒木から枝はチェーンソーで除去されます。
2 刈り込まれた木の幹、つまり丸太は、スキッダーと呼ばれる車輪付きの車両で積み込み場所まで運ばれます。丸太は長さに合わせて切断され、トラックに積み込まれて合板工場へと運ばれ、そこで丸太デッキと呼ばれる長い山に積み上げられます。
3 必要な丸太は、ゴムタイヤ式のローダーによって丸太デッキから拾い上げられ、チェーンコンベアに載せられて樹皮剥ぎ機へと運ばれます。この機械は、丸太を長軸を中心にゆっくりと回転させながら、鋭利な歯の研磨ホイールまたは高圧水噴射によって樹皮を剥ぎ取ります。
4 樹皮を剥がされた丸太はチェーンコンベアで製材所に運ばれ、巨大な丸鋸で長さ約2.5メートルから2.6メートルの断面に切断されます。これは標準的な長さ8フィート(2.4メートル)のシートの製造に適しています。これらの丸太の断面はピーラーブロックと呼ばれます。
5 ベニヤ板を切断する前に、ピーラーブロックを加熱し、木材を柔らかくする必要があります。ブロックは蒸気で処理するか、熱湯に浸す場合があります。この工程は、木材の種類、ブロックの直径、その他の要因に応じて12~40時間かかります。
6 加熱されたピーラーブロックはピーラー旋盤に運ばれ、そこで自動的に整列され、1枚ずつ旋盤に投入されます。旋盤がブロックを長軸を中心に高速回転させると、全長のナイフ刃が回転するブロックの表面からベニヤ板を毎分300~800フィート(90~240メートル)の速度で連続的に剥がします。ブロックの直径が約3~4インチ(230~305ミリメートル)に縮小されると、ピーラーコアと呼ばれる残りの木材片が旋盤から排出され、新しいピーラーブロックが所定の位置に投入されます。
7 ピーラー旋盤から出てくる長尺のベニア板は、そのまま加工することも、長い多段トレイに保管したり、ロールに巻き取ったりすることもできます。いずれにせよ、次の工程では、ベニア板を使用可能な幅(通常は約1.4メートル)に切断し、標準的な幅4フィート(1.2メートル)の合板シートを製造します。同時に、光学スキャナーで許容できない欠陥のある部分を検出し、それらを切り取って、標準幅より短いベニア板片を残します。
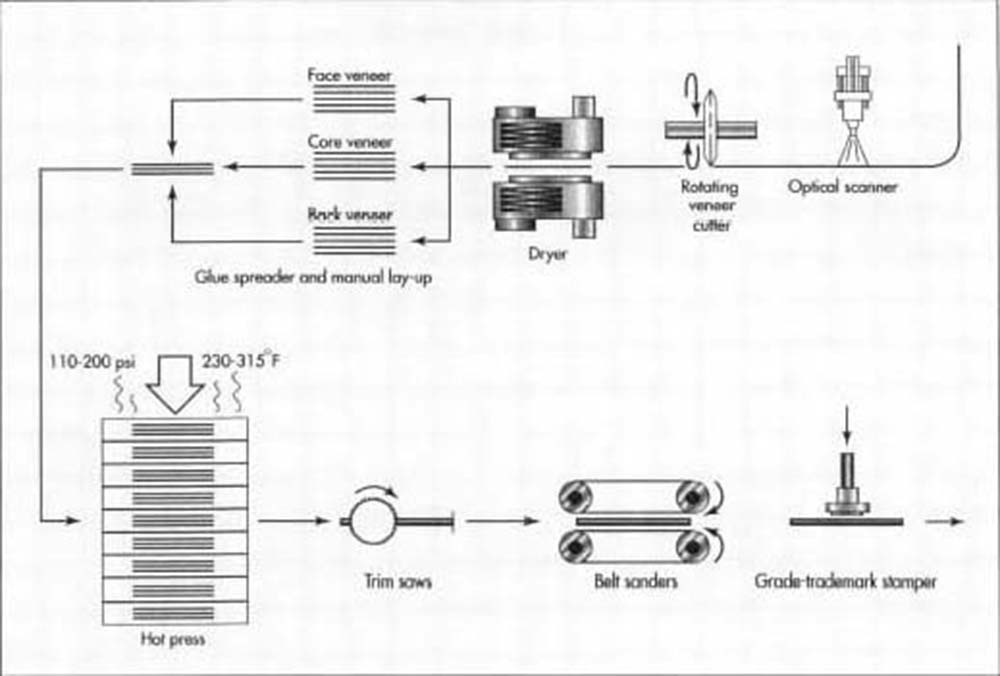
湿ったベニア板のストリップはロール状に巻き取られ、その間に光学スキャナーで木材の許容できない欠陥が検出されます。乾燥後、ベニア板は等級分けされ、積み重ねられます。選別されたベニア板は接着されます。そして、熱プレス機でベニア板を一枚の合板に圧縮し、トリミングと研磨を経て、適切な等級が刻印されます。
8 ベニヤ板は等級ごとに選別され、積み重ねられます。これは手作業で行う場合もあれば、光学スキャナーを用いて自動で行う場合もあります。
9 選別された木材は乾燥機に送られ、水分含有量を減らして収縮させ、接着前に乾燥させます。ほとんどの合板工場では、木材が加熱されたチャンバー内を連続的に移動する機械式乾燥機が使用されています。一部の乾燥機では、乾燥プロセスを加速するために、高速の加熱空気を木材の表面に吹き付けます。
10 乾燥機から出てきたベニヤ板は、等級別に積み重ねられます。幅の狭い部分には、テープや接着剤で追加のベニヤ板を継ぎ足し、外観や強度がそれほど重要でない内装層に適した状態にします。
11 横方向に取り付けられるベニヤ板の部分(3 層シートの芯材、または 5 層シートの横バンド)は、約 4 フィート 3 インチ (1.3 メートル) の長さに切断されます。
12 特定の合板製造工程に必要なベニア板のセクションが組み立てられると、各セクションを積み重ねて接着する工程が始まります。これは手作業で行うことも、機械を用いて半自動で行うこともできます。最もシンプルな3層シートの場合、まず裏面のベニア板を平らに置き、接着剤塗布機に通して上面に接着剤を塗布します。次に、芯材のベニア板の短いセクションを接着された裏面の上に横向きに置き、シート全体をもう一度接着剤塗布機に通します。最後に、接着された芯材の上に表面のベニア板を置き、シートを他のシートと重ねてプレス機に送り込みます。
13 接着されたシートは、複数枚開口部を持つホットプレス機に投入されます。プレス機は一度に20~40枚のシートを処理でき、各シートは別々のスロットに投入されます。すべてのシートが投入されると、プレス機は約110~200psi(7.6~13.8bar)の圧力でシートを圧縮し、同時に約230~315°F(109.9~157.2°C)の温度に加熱します。この圧力によってベニヤ層間の良好な接着が確保され、熱によって接着剤が適切に硬化して最大の強度が得られます。2~7分後、プレス機が開かれ、シートが排出されます。
14 粗い板は鋸引き機にかけられ、最終的な幅と長さに仕上げられます。高級な板は幅1.2メートル(4フィート)のベルトサンダーにかけられ、表面と裏面の両方が研磨されます。中級の板は、手作業でスポット研磨され、粗い部分がきれいに整えられます。一部の板は丸鋸刃にかけられ、表面に浅い溝が刻まれ、合板にテクスチャーが与えられます。最終検査の後、残った欠陥は修復されます。
15 完成したシートには、等級商標が刻印され、購入者は露出度、等級、工場番号などの情報を得ることができます。同じ等級商標のシートは束ねられ、倉庫に運ばれ、出荷を待ちます。
木材と同様に、合板にも完璧なものは存在しません。すべての合板には、ある程度の欠陥があります。これらの欠陥の数と場所によって合板の等級が決まります。建築用合板および工業用合板の規格は、米国規格協会(National Bureau of Standards)と米国合板協会(American Plywood Association)が策定した製品規格PS1によって定義されています。広葉樹合板および装飾用合板の規格は、米国規格協会(ANSI)と広葉樹合板製造者協会(Hardwood Plywood Manufacturers' Association)が策定したANSIHPMA HPによって定義されています。これらの規格は、合板の等級分けシステムを確立するだけでなく、構造、性能、用途に関する基準も規定しています。
合板は木材をかなり効率的に利用しています。つまり、木材を分解し、より強度が高く、より使いやすい形状に組み直すのです。しかし、製造工程には依然としてかなりの廃棄物が発生します。多くの場合、1本の木材に含まれる利用可能な木材体積のうち、合板に変換されるのはわずか50~75%程度です。この数値を改善するため、現在、いくつかの新製品が開発されています。
新製品の一つに配向性ストランドボード(OSB)があります。これは、丸太からベニヤ板を剥がして芯材を廃棄するのではなく、丸太全体を細長く切り刻んで作られます。細長いストランドを接着剤と混ぜ、木目が一方向に向くように層状に圧縮します。圧縮されたこれらの層は、合板のように互いに直角に配向され、接着されます。OSBは合板と同等の強度を持ちながら、価格も合板よりわずかに安価です。
投稿日時: 2021年8月10日